Too often, engineers use traditional brute force earthquake protection methods largely because of the inflated cost of seismic technologies due to a lack of responsible competition. These traditional methods are all too common not because of they are the best solution, but because they used to be the most economical. Shear walls and traditional concentrically braced frames are the norm in the industry today and this is concerning. While the design methods are often sound, the execution varies greatly from one company to the next and the lack of oversight and testing has proven dangerous in many earthquakes around the world.
Quaketek strives to makes seismic technologies more accessible to everyone. Founded by Joaquim Frazao with his expertise in aerospace manufacturing and friction dampers, Quaketek was created to improve the quality of earthquake protection technologies, all while bringing down their cost. Cost effective, reliable and tested seismic technologies offer the world a better way to protect buildings against earthquakes and our vision is to bring these technologies to the mainstream. With Quaketek you Build Safer and Spend Less
Production Facility
Located in Montreal, Canada, the main production facility is dedicated and designed for manufacturing friction dampers. Our production facility uses state of the art and automated equipment for higher precision, better quality and reduced cost. The facility also features a dedicated and climate controlled testing area where each of our dampers is individually calibrated, tested and serialized.
Quaketek is ISO 9001:2015 certified and vertically integrated, so the dampers are designed, fabricated, assembled and tested all at our Montreal facility. This provides several direct benefits:
- Allows engineers to tailor the product for a project’s technical needs without compromising manufacturability and production scheduling.
- Our manufacturing is focused on building dampers and all the equipment has been selected and customized to that end. This renders the facility highly efficient and keeps costs low and quality high.
- Building everything “in house” has improved lead times significantly. Being in control of the production schedule allows for quick turnarounds or just in time delivery depending on the customer needs.
- Our state of the art test lab with prototyping capabilities, shake table and full scale test equipment allow us to stay at the leading edge of innovation. Our Custom built testing rigs have been designed from the ground up to be optimized for production. This allows us to test every damper at full stroke and load without increasing the cost of the product and exceed the testing requirements of many international building codes.
Background & History
Quaketek’s history goes back to 1987 when Mr.Frazao developed the friction surface technology which limits the effects of creep, corrosion and stick slip in seismic friction dampers. The company Mr. Frazao co-founded, Mechtronix Systems inc. has since manufactured dampers used in hundreds of buildings around the world. Quaketek has continued in the tradition of high quality friction dampers using the same methods and further improved on precision and quality by investing in our dedicated production facility.
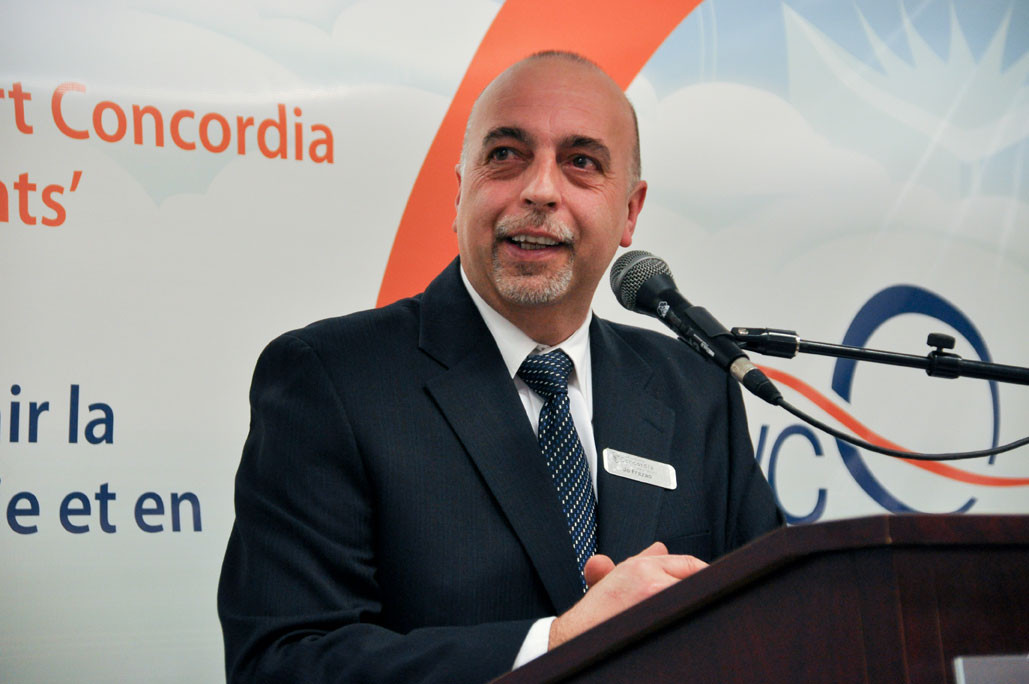
Excerpt of an interview with our founder, Joaquim Frazao:
I was studying Mechanical engineering, and working on my Masters degree at Concordia University in Montreal. It was here that I realized the numerous interdisciplinary challenges being faced by engineers at the time. I met a group of fellow students of various engineering backgrounds and together we founded Mechtronix Systems inc. with a goal of developing interdisciplinary solutions to engineering challenges, hence the name Mechanical Electronics, Mechtronix. It was in these early days that an interesting opportunity arose, a well known professor at Concordia University had a challenging problem. He had patented a friction damper but needed experts in manufacturing and materials to manufacture it. With a first order for 150 friction dampers to be installed in the Concordia Library building on de Maisonneuve, I quickly went to work trying to figure out how to deliver that first production run, and just as quickly realized that there was a lot of room to improve!
Well the original idea (and patent) for the seismic friction damper was to use brake pads or bronze plates to generate friction however the challenge was that the slip load would change over time due to creep in the friction pad and the set load in the bolts. Being involved in aerospace and having studied mechanical engineering I was familiar with a number of methods to control friction in aerospace. With a lot of curiosity and an innate need to “find a better way” I came up with methods and a manufacturing processes which resulted in friction slip joints with minimal longterm creep, no risk of galvanic corrosion and no stick-slip behavior. These innovations allowed for an important improvement to friction damper technologies, a damper that could maintain a stable slip load throughout the lifetime of a building. Using these new methods, Mechtronix was able to maintain exclusivity in manufacturing for a prominent brand and we built thousands of dampers which today are used in buildings around the world.
Well, Mechtronix was mostly focused on another interdisciplinary challenge, flight simulation devices. The company was highly successful in innovating in the simulation market and helped to make flight training more accessible, reducing the cost a full flight simulator by more than 50%. When the company was sold, and became solely focused on aerospace we knew that the damper manufacturing had to continue. So, in 2015, I partnered with my sons and founded Quaketek with a simple objective: Make earthquake protection easy and accessible, to every person living in a seismic region. The basic idea, do for earthquake safety what we did for aviation safety.
The concept was simple, establish a purpose built facility for manufacturing friction dampers in order to obtain economies of scale, use the same manufacturing methods and techniques developed over the last 30 years, improve overall quality and consistency and innovate some more! These economies of scale can then be used to reduce the current market price of friction dampers rendering them competitive with traditional construction and one-time use (yielding) technologies such as BRBs. We want to innovate further because there are many other industries where friction technologies can help protect people, and well, because we can’t help but constantly try to improve…
We see two main challenges to growing the usage of friction dampers. The first challenge being education. Many people believe that seismic protection technologies are expensive and or difficult to use, while true for some technologies, the friction damper tends to be the opposite. Friction damper technologies are not velocity dependant and stable slip loads making them easy to design with. With building codes now providing guidance on ductility factors for friction dampers, (e.g. Chile’s dissipation chapter NCh34-11) we believe that more engineers will use these guidelines to integrate seismic dampers.
The second main challenge is economic. Developpers and engineers alike, sometimes believe that integrating dampers will increase the overall cost of their project. In reality, friction dampers tend to decrease structural costs by reducing the demand on the main structural elements. Because the dampers dissipate seismic energy, columns, beams and foundations need only resist a smaller force. The savings in structural elements are usually enough to pay for the dampers installed and still see savings.
Of course, the underlying challenge remains staying relevant in an every changing world of technology and so we continue to carefully listen to our customer needs and invest heavily in R&D to address their everyday challenges.